Inside Productization: A Toybox for Collaborative and
Modular Construction
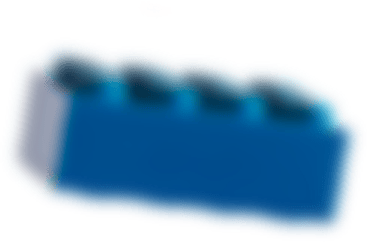
There’s a big difference between making a house with toy building blocks and a real-world construction project. Or is there?
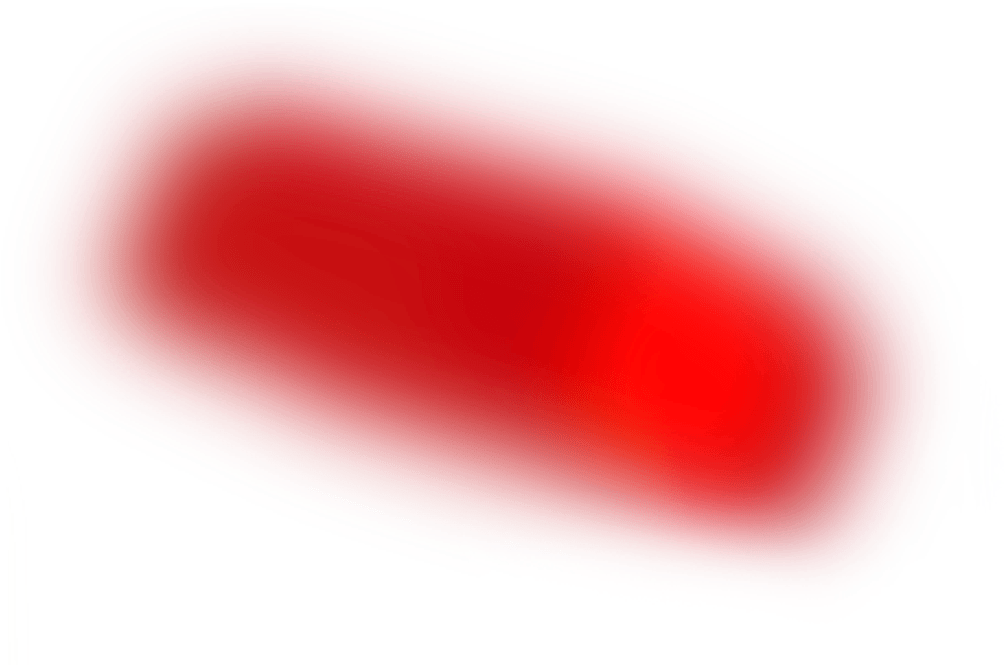
Traditional construction processes have long been highly fragmented, involving multiple stakeholders – from architects to materials suppliers to builders – across the lifecycle of a typical project. This can make it difficult to deliver projects at the best of times. But doing so whilst navigating today’s biggest strategic challenges, from the global skills shortage to rising material and labor costs to ever evolving ESG regulations, is a huge task.
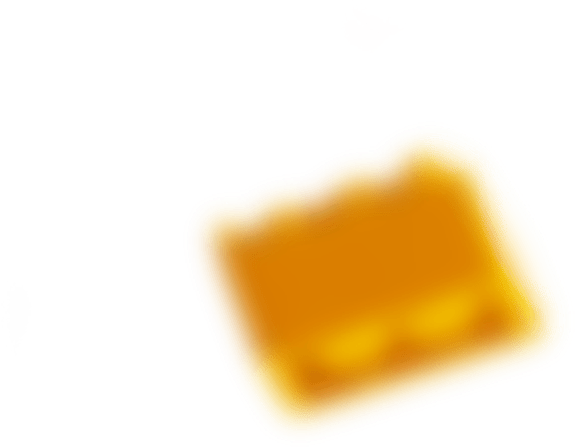
Digital transformation in construction is sorely needed, and after years of slow progress, it is finally happening. At the vanguard of this revolution is productization, which aims to transform construction elements from static, bespoke objects into generative assets, allowing for more convenient, cost-effective, and flexible approaches to construction.
Modern construction challenges, modular construction solutions
Put simply, productization involves isolating and defining the processes by which given components are made – from pre-cast walls to window frames to underfloor wiring – and making that process easily repeatable.
As Marty Doscher, Architecture & Construction Digital Transformation Leader, Dassault Systèmes, explains: “The general idea is to break the building into a series of products, that can be easily duplicated or modified for different needs.”
The process of productization works as follows:
- 1.
Creating Virtual Construction Bricks:
First, given construction processes are defined and organized into groups called “virtual construction bricks”. These bricks are generative and adaptive – that is, they can be modified according to the parameters of individual projects. - 2.
Database Integration:
Then, these bricks are loaded onto a database, where they can then be licensed as needed. A builder could select, for example, a staircase from one supplier and floor from another. - 3.
Virtual Building Integration:
Bricks are then integrated into a virtual building, allowing builders to optimize for time, cost, and materials. The generative nature of these bricks means that they can be easily adapted to meet different physical, material or process needs. - 4.
Manufacturing and Assembly:
Once selected, physical elements are manufactured at small-scale micro-factories, transported to worksites, and assembled according to standardized instructions – saving on the cost and complexity of worksite management and coordination.
In order to be effective, productization needs a secure digital platform to serve as an effective database and marketplace through which modules can be stored, exchanged, managed, and integrated in real-time. Not only do virtual twins provide that environment; but they also provide a medium for continuous improvement, where learnings from each build can be fed iteratively back into the data for each “brick”.
Example apartment-project-construction duration, traditional vs off-site 3-D volumetric, months
Prefabrication transformed
What differentiates productization most dramatically from older approaches to prefabrication is the power of digital technology and algorithmic, generative design to combine the bespoke and the standardized.
“Productization is a bit like a recipe book. We might not have the time to develop the expertise of a top chef. But we can buy their cookbook, and then access the tricks and recipes they have developed over a lifetime,” says Doscher. “However, what if a recipe is for four, but we need to feed eight? What if we need to replace one spice with another?”
By combining productization with the power of digital technology, virtual twins allow for this flexibility letting businesses to tailor their approach to specific project needs, modelling the structural and cost impacts of different materials or components at pace.
“The general idea is to break the building into a series of products, that can be easily duplicated or modified for different needs.”
Modular power from modular structures
Modular construction is also being used in other sectors, such as energy, to help navigate similar issues around cost and complexity.
For example, Small Modular Reactors (SMRs) and Advanced Modular Reactors (AMRs) will be crucial to meeting Net Zero targets as many nations pledge to triple nuclear generation capacity by 2050¹.
“With SMRs and AMRs, we can standardize and industrialize our approach to building nuclear capacity, cutting cost and risk.” says Audrey Goulven, Sustainable Infrastructure and Clean Energy Director, Dassault Systèmes. “And because of their small size and modularity, they can be deployed much more flexibly, with new units added as needed.”
Virtual twins can speed up this process. “Virtual twins bring together and leverage the data from the whole lifecycle of development of SMRs and AMRs, from design to operation, bringing high levels of collaboration, knowledge preservation, and standardization to the overall process of construction and operation,” says Goulven.
Solving the issues of speed, cost and consistency, whether in the power industry or in the construction industry, is central to making infrastructure development faster and more sustainable. Productization, combining modularization, standardization and industrialization, and leveraging the power of virtual twins, can play a critical role in allowing the industry to transform outmoded practices and processes, and meet the demands of the future.
PREPARING TODAY'S STUDENTS FOR PRODUCTIZATION
Productization will not replace long-standing design, engineering and construction techniques, but it will augment them, enabling businesses to produce the buildings we need faster, more sustainably, and at scale. Dassault Systèmes is actively working with education institutions such as the University of Southern California (USC), where they are giving future engineers hands-on experiences with the virtual twins approach that will be used to deliver tomorrow’s productization solutions.
“Through its education of the next generation of change makers, Civil and Environmental Engineering – CEE at USC - is equipping civil and environmental engineers with the necessary skills to harness technology and lead transformative initiatives for a better, more sustainable future.” says Burcin Becerik-Gerber, Dean's Professor of CEE at USC Viterbi USC. Rethinking the skills of the future professionals in the industry and its role in innovation is key.
It's just one of the many ways that 3DEXPERIENCE Edu is supporting academic institutions in their transformative mission to provide the skillsets that will not just be needed by today’s engineers, but will support the practice of radical new methodologies – like productization – well into the future.
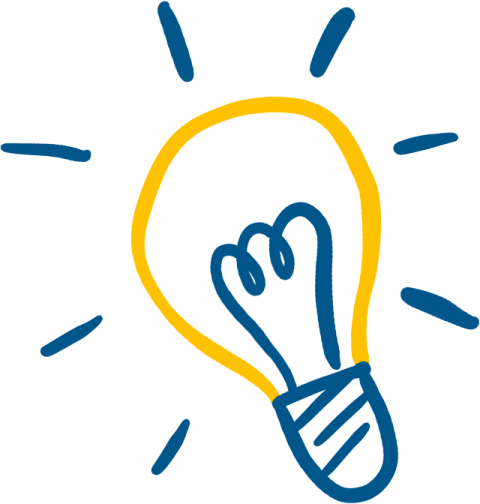
Insights on Infrastructure & Cities
A modular building is a structure constructed using prefabricated sections, or modules, which are manufactured in a factory setting and then transported to the building site for assembly. These modules can be combined in various configurations to create a wide range of building designs.
Aspect
Modular Construction
Non-Modular Construction
Construction Process
Modules are prefabricated in a factory and assembled on-site
Built entirely on-site from the ground up.
Build Time
Generally faster due to simultaneous site work and module construction.
Typically, slower due to sequential on-site work.
Quality Control
Higher quality control in a factory setting.
Variable quality control, dependent on-site conditions.
Weather Impact
Less affected by weather delays since most work is done indoors.
Highly susceptible to weather delays and conditions.
Cost
Potentially lower due to efficiency and reduced labor costs.
Often higher due to longer build times and labor.
Flexibility and Scalability
High flexibility; modules can be added or reconfigured easily.
Less flexibility; modifications can be complex and costly.
Sustainability
More sustainable with reduced waste and energy efficiency.
Typically more wasteful and less energy efficient.
Customization
Customization is made possible through generative design and standardized processes.
One-off designs and processes cause cost overruns and delays.
Transport and Logistics
Requires transportation of large modules to the site.
Materials transported to site in smaller batches.
Structural Integrity
Strong, but module connections need careful design and inspection.
Strong, continuous construction can offer robust integrity.
Modular construction is better because it significantly reduces build times and costs by allowing simultaneous off-site module fabrication and site preparation, ensures higher quality control through factory settings, and offers greater flexibility and sustainability by reducing waste and environmental impact.
The three types of modular construction are:
Permanent Modular Construction (PMC): These are modules that are intended to remain in one location for the life of the building. PMC is used for a wide range of building types, including residential, educational, healthcare, and commercial buildings.
Relocatable Buildings (RB): These structures are designed to be reused or repurposed multiple times and transported to different sites. They are often used for temporary applications such as classrooms, construction site offices, and emergency shelters.
Hybrid Modular Construction: Combines modular construction with traditional construction methods. Some parts of the building are constructed using modules, while others are built on-site.
Modular construction offers some advantages, it enables faster build times and lower costs by allowing simultaneous off-site module fabrication and site preparation. It ensures higher quality control through factory settings and provides greater flexibility and sustainability by reducing waste and environmental impact. These benefits make it a more efficient and environmentally friendly alternative to traditional construction methods.
Examples of modular construction include residential homes, such as prefabricated houses that are assembled on-site from factory-made modules; industrial buildings, like factories, mission; critical facilities, like data centers; and healthcare facilities, including modular hospitals and clinics designed for rapid deployment. Additionally, educational buildings, such as modular classrooms and school extensions, showcase the versatility of this construction method.